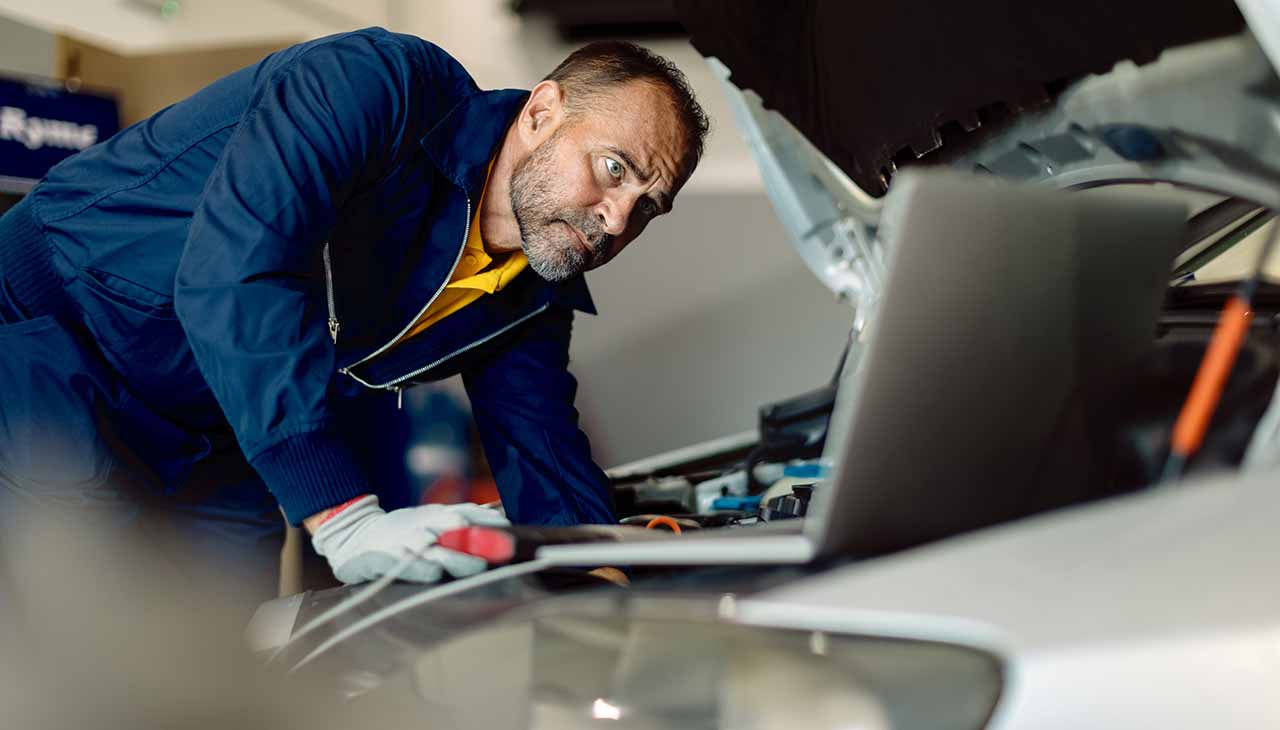
Cómo Evitar Errores Comunes en el Mantenimiento de Vehículos Industriales
El mantenimiento adecuado de los vehículos industriales es crucial para garantizar su seguridad y eficiencia operativa. Sin embargo, muchos gerentes de flota, operadores de vehículos industriales y técnicos de mantenimiento cometen errores que pueden resultar costosos y peligrosos. En este artículo, exploraremos los errores más comunes en el mantenimiento de vehículos industriales, las consecuencias de estos errores y las mejores prácticas para evitarlos. Además, compartiremos estudios de caso de empresas que han mejorado sus operaciones mediante el mantenimiento adecuado.
La Importancia del Mantenimiento Adecuado
El mantenimiento adecuado de los vehículos industriales no solo asegura su funcionamiento eficiente, sino que también previene accidentes y reduce el tiempo de inactividad. Los vehículos industriales son el corazón de muchas operaciones y su correcto mantenimiento es vital para el éxito de la empresa. Un programa de mantenimiento bien estructurado puede prolongar la vida útil de los vehículos, mejorar la seguridad y reducir costos.
Errores Comunes en el Mantenimiento
Ignorar las Inspecciones Regulares
Uno de los errores más frecuentes es no realizar inspecciones regulares. Las inspecciones periódicas permiten detectar problemas antes de que se conviertan en fallos graves. Saltarse estas inspecciones puede resultar en averías inesperadas y costosas reparaciones.
Las inspecciones deben incluir una revisión completa de los componentes clave, como el motor, los frenos y los sistemas hidráulicos. Documentar los hallazgos y tomar medidas correctivas inmediatas es fundamental para mantener la flota en buen estado.
Lubricación Incorrecta
La lubricación adecuada es esencial para el funcionamiento suave de los componentes mecánicos. Sin embargo, muchos técnicos utilizan lubricantes inadecuados o no siguen el programa de lubricación recomendado por el fabricante. Esto puede provocar un desgaste prematuro y fallos mecánicos.
Es importante utilizar el tipo y la cantidad correcta de lubricante según las especificaciones del fabricante. Además, se debe prestar atención a los intervalos de lubricación y ajustarlos según las condiciones de operación.
Ignorar las Señales de Advertencia
Las señales de advertencia, como luces de alerta en el tablero, ruidos inusuales o cambios en el rendimiento, nunca deben ser ignoradas. Estas señales indican problemas potenciales que, si no se abordan a tiempo, pueden llevar a fallos mayores y paradas inesperadas.
Implementar un sistema para reportar y actuar rápidamente ante cualquier señal de advertencia puede prevenir daños costosos y mejorar la seguridad.
Consecuencias de los Errores
Tiempo de Inactividad
El tiempo de inactividad es una de las consecuencias más directas de los errores de mantenimiento. Cuando un vehículo industrial no está disponible, las operaciones se detienen, lo que afecta la productividad y puede causar retrasos en la cadena de suministro.
El tiempo de inactividad también puede resultar en horas extras para los empleados, costos adicionales para arrendar equipos de reemplazo y pérdida de ingresos.
Riesgos de Seguridad
Los errores de mantenimiento pueden aumentar significativamente los riesgos de seguridad. Un componente defectuoso puede causar accidentes que pongan en peligro la vida de los operadores y otros empleados. Además, los incidentes de seguridad pueden resultar en sanciones legales y dañar la reputación de la empresa.
Implementar y seguir estrictamente un programa de mantenimiento puede reducir estos riesgos y crear un entorno de trabajo más seguro.
Costos de Reparación Elevados
Ignorar problemas pequeños puede llevar a reparaciones más costosas en el futuro. Por ejemplo, un sistema de frenos que no recibe mantenimiento adecuado puede necesitar una reparación completa en lugar de un simple ajuste. Estos costos pueden acumularse rápidamente y afectar el presupuesto de mantenimiento.
Un enfoque proactivo en el mantenimiento puede reducir estos costos a largo plazo y optimizar los recursos.
Mejores Prácticas en Mantenimiento
Establecer un Programa de Mantenimiento Integral
Un programa de mantenimiento integral es la base para prevenir errores comunes. Este programa debe incluir inspecciones regulares, mantenimiento preventivo y registros detallados de todas las actividades de mantenimiento.
Utilizar software de gestión de flotas puede ayudar a automatizar y organizar estas tareas, asegurando que nada se pase por alto.
Capacitar al Personal
La capacitación adecuada de los técnicos y operadores es crucial para el mantenimiento exitoso. Todos deben estar familiarizados con los procedimientos de mantenimiento, el uso correcto de herramientas y equipos y cómo interpretar las señales de advertencia.
Ofrecer formación continua y mantener a los empleados actualizados con las últimas técnicas de mantenimiento puede mejorar la eficiencia y la calidad.
Utilizar Herramientas y Piezas Adecuadas
El uso de herramientas y piezas adecuadas es fundamental para el mantenimiento efectivo. Las piezas de repuesto deben cumplir con las especificaciones del fabricante y las herramientas utilizadas deben ser apropiadas para la tarea.
Invertir en herramientas de calidad y mantener un inventario de piezas esenciales puede minimizar el tiempo de inactividad y mejorar el rendimiento de los vehículos.
Considerar la Externalización
En algunos casos, externalizar el mantenimiento a profesionales puede ser una opción rentable y eficiente. Los proveedores de servicios de mantenimiento especializados cuentan con la experiencia y los recursos necesarios para realizar tareas complejas y mantener los vehículos en óptimas condiciones.
Evaluar los costos y beneficios de la externalización puede ayudar a las empresas a tomar decisiones informadas sobre el mantenimiento.
Estudios de Caso Exitosos
Ejemplo 1: Programa de Mantenimiento Intensivo en una Compañía de Transporte
Una compañía de transporte implementó un programa de mantenimiento intensivo que incluía inspecciones diarias y semanales, así como mantenimiento preventivo cada seis meses. También se capacitó a los operadores para realizar controles básicos antes y después de cada turno.
Como resultado, el tiempo de inactividad se redujo en un 20%, las reparaciones costosas disminuyeron y la seguridad mejoró significativamente.
Ejemplo 2: Externalización del Mantenimiento en una Empresa Logística
Una empresa logística decidió externalizar su mantenimiento a un proveedor de servicios especializado. Esto les permitió enfocarse en su actividad principal y dejar el mantenimiento en manos de expertos.
Con la externalización, se logró una mayor eficiencia y un menor tiempo de inactividad, lo que resultó en ahorros significativos para la empresa.
Conclusión
En resumen, los errores de mantenimiento pueden tener consecuencias graves para las empresas que utilizan vehículos industriales. Establecer un programa integral de mantenimiento, capacitar al personal adecuadamente y utilizar herramientas y piezas adecuadas son algunas medidas clave para prevenir estos errores. Además, considerar la externalización puede ser una opción viable para optimizar el mantenimiento y mejorar la eficiencia. Al seguir estas mejores prácticas, las empresas pueden minimizar los costos y riesgos asociados con el mantenimiento de sus vehículos industriales. El mantenimiento adecuado es una inversión en la seguridad, productividad y rentabilidad a largo plazo de cualquier empresa que dependa de vehículos industriales para sus operaciones diarias. Por lo tanto, no se deben ignorar las señales de advertencia y se debe actuar rápidamente ante cualquier problema para evitar consecuencias negativas en el futuro. ¡No subestimes el poder del mantenimiento preventivo! Con un enfoque proactivo, puedes mantener tus vehículos en óptimas condiciones y maximizar su rendimiento. Así que sigue estas mejores prácticas y asegúrate de tener un programa de mantenimiento sólido en marcha para proteger tus activos y garantizar el éxito continuo de tu empresa.